Punching Formed and Extruded Parts
Punching holes in aluminum extrusions, shaped parts, or brake-formed and roll-formed components can be challenging — but not with UniPunch. Our modular tooling system is engineered to handle the complexities of shaped and extruded profiles, making hole punching fast, accurate, and efficient.
- Window Extrusions
- Metal Buildings
- Lighting
- Seating
- Interior and Exterior Doors
- Seating
- Appliances
- Furniture
- Storage Systems
- Shelving
- Cabinetry
- Trailer Extrusions
- Marine
- Lift Gates
- Truck Beds
- Fencing/Animal Enclosures
- Feeders
- Radiators
- Tractors
- Combines
Punch Multiple Holes-Fast
In just one stroke, you can punch multiple holes with consistent accuracy, dramatically reducing production time and labor. Unlike CNC machines, which require programming, or ironworkers that punch one hole at a time with manual feeding, UniPunch offers a faster, easier solution that operators can master quickly. No complicated setups, no delays—just efficient, cost-saving performance.
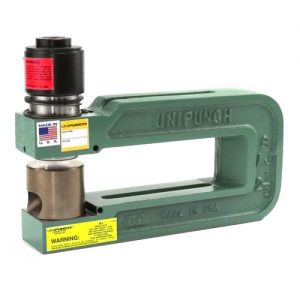
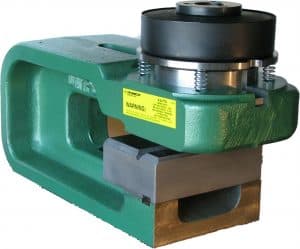
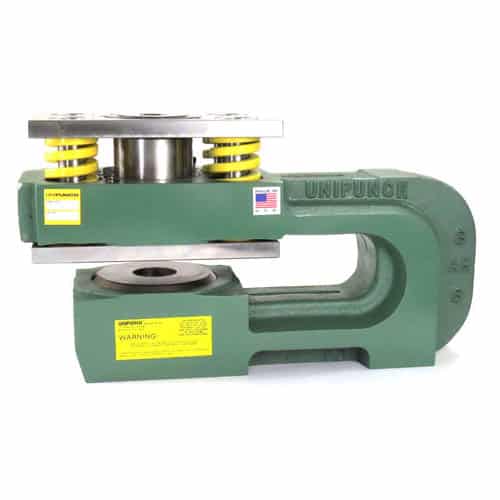
Punch Aluminum Extrusions
UniPunch tooling is ideal for aluminum extrusions up to 1/4″ thick. Our AJ Series and Feed Clearance Units are specifically designed for this type of work. The pedestal die design allows punching close to a leg, wall, or edge of complex profiles.
“Using UniPunch pedestal dies is the only way we can punch holes in these complicated extrusions. We have tried many other things before, but this is the best way.” -Libio Ramirez, Ultra Industries
Why Choose UniPunch over Die Sets?
Lead Times
Die sets often take 6+ weeks to manufacture. UniPunch systems are typically ready to ship in just one week.
Maintenance
Die sets require disassembly for sharpening. UniPunch tooling allows easy replacement of punches and dies—right on the press or shop floor.
Upfront Costs
UniPunch systems can save thousands compared to the cost of custom die sets.
Manufacturers Love Saving Time with UniPunch
Frequently Asked Questions
Anywhere from .0937″ to 3.000″
Yes, UniPunch tooling is highly adaptable and can accommodate a wide range of extruded and shaped parts, including angles, channels, tubes, and aluminum extrusions. UniPunch units can be customized for non-standard profiles and various material thicknesses. The tooling can be adjusted to work with both small and large extrusions and complex shapes.
UniPunch tooling uses precision-machined components and guides that ensure accurate hole placement, even in complex shapes. The tooling system features self-contained stripping assemblies that align punches and dies for consistent results, ensuring that holes are punched precisely where needed on extruded and shaped parts. The tooling is designed to maintain high accuracy across multiple parts, making it ideal for both small and large production runs.
UniPunch works with customers to customize tooling solutions for extruded parts. The process typically involves sending a drawing or sample of the part, after which UniPunch engineers will recommend and modify standard tooling or create custom tooling to fit your specific needs. The tooling can include special pedestal dies or die adapters that allow punching close to the edges of angles and channels, ensuring flexibility in handling various part shapes and configurations.